How to start Woven Sacks Production Business in Nigeria
As the demand for durable and eco-friendly packaging solutions
continues to rise, understanding how versatile PP woven sacks
are crafted has never been more crucial. Woven bags
manufacturing process involves using premium polypropylene (PP)
resin to create durable woven fabric, which is then printed,
cut, and stitched into bags of various styles and sizes.
Market Potential: The major users of woven sacks are fertilizer,
sugar, animal feeds, and cement. Starches, pesticides,
detergents and many other industrial bulk items are also being
packed in woven sacks. HDPE strips also used for deck chairs,
etc. PP strips used for marine rope manufacturing.
With the introduction of circular looms, cost of production has
come down drastically and making these sack more preferable now.
Demand is ever growing with more and more factories preferring
woven sacks for packaging. 90% of the production is consumed in
the domestic industry while a little is being imported to border
countries. With small and medium scale industries/ agricultural
projects springing up, the demand also increases.
The market cuts across the whole parts of the country and
neighboring African countries.
Manufacturing Process: First the tape is produced through the
tape extrusion machine.
This tape is fed to knitting machine to form cloth on circular
weaving machine.
Cloth thus formed is cut to required dimensions and stitched to
size.
Printing is also done as per requirement and plan according to
IS standards to meet customers’ requirements.
Location of the Project
The project can be located in any part of the country either in
the Northern and Southern Nigeria.
Project Estimation
Unit runs on single shift 25days per month; Wastage of raw
materials estimated is around 2%; Number of bags per kg
depending on the density used; uninterrupted power availability
is assumed, therefore there should adequate arrangement for
power generating set and other alternatives to power..
450MT production capacity is estimated to be economically viable
for a small scale industry.
Raw-Materials: 40T HDPE/PP granules; printing accessories;
packing accessories. These raw materials are all available
within the country.
Utilities: The project requires 300kva generator set, 11kva
transformer; Electricity & water
A
typical process is as follows: Pre-press preparation:
Specialized graphic design software is used to create text,
images, and logos that will be printed on the PP woven bags.
Once the design is finalized, it’s converted into a format that
can be used for printing, such as a digital file or a plate.
Plate creation: If traditional flexographic or gravure printing
is used, plates need to be created. These plates are typically
made of metal or other materials and are engraved or etched with
the design. The plates are then mounted onto the printing press.
Ink prep: Ink is mixed according to the required color and
viscosity specifications.
Printing: We then feed the woven bags into the press, where the
ink is transferred onto the bags using the plates or other
cylinders. This is repeated until all the different colors or
layers of ink are applied.
Dry-cure: The ink is cured or dried after each application,
depending on the method used.
Post-press finishing: After printing we use heat-setting to cure
the ink and improve its durability and apply a varnish or
coating for added protection or glossiness.
Quality control: Throughout this process, our QC measures ensure
that the printed PP woven bags meet the desired color accuracy,
print clarity, and other specs. Any defects or issues are
identified and addressed to ensure a high-quality finished
product.
Cutting: Cutting the material can be done by either hot or cold
cutting: Heat Cutting
Heat cutting melts and seals the PP woven fabric edges to create
clean and sealed cuts. The general heat-cutting process for PP
woven bulk bags is: Preparation: The woven fabric is first laid
out in multiple layers, and the bag panels are aligned according
to the desired bag size and shape. The layers are stacked and
held together securely to prevent movement during cutting.
Tool setup: A heat cutting tool, such as a hot knife or a heated
wire, is set up and adjusted for the desired temperature and
cutting depth. The temperature is controlled to ensure precise
cutting without causing excessive melting or scorching of the
fabric.
Quality
control: We ensure that the cuts are accurate, clean, and free
from defects. This involves checking for proper cutting depth,
sealing quality, and bag integrity.
The biggest difference between the two processes is the
elimination of heat during cutting. Instead, a knife or blade is
used to mechanically cut through the fabric without applying
heat.
One of the benefits of cold cutting over using heat is the
reduced energy consumption for the manufacturer. However, this
can only be applied to material that has been coated.
Cold cutting also reduces the risk of fraying, which can
compromise the bag’s strength and durability. Even so, this
doesn’t mean that heat cutting causes a weakness, since we
ensure all our bags maintain the same integrity levels.
Packaging:
Once the bags pass the inspection, they’re packed in our secure
and controlled environment. This involves stacking the bags,
bundling them together, or packing them in boxes, bales, or
pallets, depending on the customer’s needs. Proper packaging is
important to protect the bags from damage during transportation
and storage and to ensure they are ready for distribution or
sale.
Labeling: Depending on
the specific requirements or regulations, the bags are labeled
with relevant information, such as product details, brand name,
size, weight, safety instructions, and other necessary
information for identification and traceability.
Financial Implications
The cost of the project depends wholly on the scale the
investors want to run for a start. Generally, the feasibility
studies will be carried out, putting the proposed location into
consideration in determining the actual cost of establishing the
proposed project. You can run the project on small, medium and
large scale.
Investment Analysis
Payback Period: Within 2years
Rate of Returns on Investment: 40.4 %
Break Even Point : B.E.P 55.0%
Profitability:
The project is very profitable and raw materials could be
obtained within the country.
Get our Practical Guide on how to start Woven Sacks Production
Business in Nigeria. Detailed structure of the production
processes, Including personnel and manpower requirements, Plant
layout, Raw materials sourcing, Marketing Techniques etc, will
be embodied in a Comprehensive Feasibility Report for interested
investors.
Click here to fill our application form:
https://forms.gle/jt7DaqkmobimT5PX8
One on one practical training with ongoing support
from our resource person. Well-crafted training
initiatives aim to close skill gaps, thus boosting
individual performance. The success of this program
reflects our shared commitment to creating a better
future for our participants The trainees are evaluated
at the end of the training period to ascertain the
reliability of such training so as to assist in the
provision of necessary instrument needed for starting
the business or trade. Training is built on an active,
experimental and practical learning sessions. Our expert
advice is unique, actionable, and impossible to
replicate. No one else can provide the tailored insights
we offer, designed specifically for your success
.Imagine having a roadmap tailored just for you, guiding
you step by step toward your
career goals. Attendees will receive certificate
of participation at the end of the Training
Click here to fill our application form:
https://forms.gle/jt7DaqkmobimT5PX8 |
Our motivation is to see every Nigerian benefit from our
Unique Income opportunity, specially focused towards a
sustainable, entrepreneurial, and innovative future by
connecting them to new ideas and skills
Browse through our highly resource information
over 500 Business ideas.
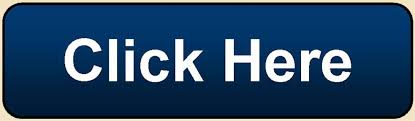
|
This guide is designed to help business people including Micro,
Small and Medium Scale Entrepreneurs navigate the legal and
regulatory considerations relevant to starting-up and doing
business in Nigeria.CLICK HERE |
Creating
multiple streams of income can be a strong way to improve
your personal finances. Whether you’re trying to boost your
savings or build toward a goal, this is a move that many of
the most financially successful Nigerians make.CLICKHERE |
|
|