How to Set Up a Pet Bottle Manufacturing Business in Nigeria
As the world invents more and more different devices to
manufacture plastics , with increasingly sophisticated
requirements, new Plastics bottles
are developed to meet the diversifying needs of industry
Innovations and mandated health, safety, and environmental
concerns. This inevitably increases complexity in manufacturing
and opportunities available. However to succeed in the industry
requires
Plastic bottles have become an indispensable part of our daily
lives, serving as containers for various beverages, household
products, and more. The mass production of these ubiquitous
items relies on highly sophisticated industrial processes and
specialized equipment. In this article, we will delve into the
intricate world of plastic bottle production, exploring the
technologies and machinery that make it all possible.
Raw materials Requirement: The major material used is the PET
Preforms. The plant has the capacity to produce PET bottles from
PET Preforms. Other materials includes bagging nylons.
Machinery requirement:
4 Cavity Semi-automatic PET Blowing machine With Air
Compressor,
Chilling System, Standards Bottle Moulds, Spares, 20KVA
Generating Set,, Safety equipment, Delivery van
There are currently two methods for the production of PET
plastic bottles. One is to use an automatic PET bottle blowing
machine to complete all the steps from PET raw materials to
formed PET bottles. Another production method is to use a
two-step method, first use an injection molding machine to make
a PET preform, and then blow the bottle through the mold of the
bottle blowing machine. The first method can be produced by a
fully automatic blow molding machine, but the cost of the
equipment is relatively expensive. Generally, large plastic
bottle processing plants will purchase plastic bottles using
this method. The two-step method is the method that most
companies often use to make plastic bottles.
Extrusion Blow Molding - In extrusion blow molding a round,
hollow tube or parison is formed by an extruder. A mold cavity,
composed of two halves, closes around the parison and pinches
off one end. Compressed air expands the parison to conform
against the cold mold cavity walls. When sufficiently cool, the
mold opens and the container is removed and trimmed of excess
plastic or flash. Flash, a basic characteristic of extrusion
blow molding, is formed when the parison is pinched off by the
mold. Since most resins can be reprocessed, the flash is not
wasted but is used as "regrind."Wall distribution, thickness,
and weight can be controlled by parison programming. While the
parison is extruded, programming changes in the relation of
mandrel and die can be used to shift material from heavier,
stronger areas to lighter, weaker areas. This method aids
significantly in maximizing container performance and minimizing
container weight and cost.
Injection Blow Molding - The process of injection blow molding
(IBM) is used for the production of hollow plastic objects.
Injection blow molding is performed in basically three stages.
At the first stage, melted plastic is injected into a mold
cavity to produce a preform parison. The preform is shaped like
a test tube, but with a molded screw finish at the top. The
preform is then transferred to the second, blow-molding stage.
Air is blown through a core pin to expand the preform against a
cold mold cavity. The container is then transferred to the third
station for ejection.
Two main types of processes exist:
One-step injection molding – the melted polymer is injected into
the final shape of the container in a cold mold, it's then
released.
Two-step injection molding – the first step in the injection of
melted plastic in a mold, resulting in the creation of a
preform. The cold preform is then taken onto another machine,
enclosed in a mold, heated, stretched with a pin to reach the
desired length and then blown in the shape of the chosen mold.
Stretch Blow Molding - Stretch blow molding uses either the
injection or extrusion blow molding process as a basic
foundation. In either case, a preform parison is molded and then
transferred to a blow molding cavity. The parison is stretched
biaxially during blow molding to orient and align the molecules.
This orientation improves the gas barrier, stiffness, clarity
and impact strength of the container. As a result, containers
can be reduced in weight.Resins which can be stretch blow molded
include PET, PVC and Polypropylene. PET has by far the most
common use in carbonated beverage containers.
Injection Molding - Injection molded containers can be straight
sided or tapered, narrow or wide mouth shapes such as jars,
tubs, and vials. Material is injected into a cavity where
pressure forces the resin to conform to the mold body.
Containers are capable of holding to a tighter dimensional
tolerance, and are more uniform in wall distribution. A wide
variety of resins can be processed via the injection molding
process, the most popular being polypropylene, styrene, and
polyethylene.
Multi-Layer Bottles ---- Co-Extrusion - The newest of bottle
blowing technology, co-extruded multi-layered bottles bond
various plastic resins together with tie layers to produce
bottles with barrier and heat-stable qualities suitable for use
with hot-filled, hermetically sealed food products. Currently
EVOH (ethylene vinyl alcohol) is used as the central layer
because of its barrier properties. Polypropylene or polyethylene
is used as the inner and outer walls because of their heat
tolerance and clarity.The hot-fill process creates a vacuum
which will draw in the side walls of a plastic container. This
effect must be compensated for in bottle design, either by using
an oval shape which will cloak the indentation or by employing
strengthening ribs or panels in a round bottle design.Possible
applications include: juices, sauces, jams, toppings,
mayonnaise, and pickled products.
How to make PET plastic bottles?
1. First, heat the PET raw material to melt it into a molten
state, and then put it into the tubular mold of the PET preform
making machine. The PET has the same shape as the mold called a
parison, and after the system cools, the parison is cut to the
correct length.
2. Heat the prepared preform and put it into the mold of the
blow molding machine. A steel rod is placed inside the preform
and high pressure air is blown to stretch the preform into the
shape of the mold.
3. After blow molding, the bottle is quickly cooled and removed
from the mold.
4. There may be some excess material seepage during the
production process, so trimming is required.
5. The trimmed PET bottle is the bottle that is often used in
our daily life.
Startup Capital: The total production Machinery cost is about 8
million Naira, Excluding Cost of Generating set and Delivery
Van. Working capital is projected for 42million Naira which can
however be higher depending on the financial capacity of the
promoter. Gross margin from the plant is projected at 15 million
Naira and profit before tax about 8 and 10 million Naira in the
first and second year respectively. Payback is within 24 months.
The demand for PET plastics is estimated to rise at about seven
percent (7%) annually over the next ten (10) years. With the
growing demand for carbonated soft drinks, water and edible oil,
PET Preform bottles are also increasing in demand.
The production of plastic bottles on an industrial scale is a
marvel of modern engineering and automation. From the careful
preparation of raw materials to the precision molding,
inspection, and packaging, the entire process is a testament to
the integration of technology and innovation. As we continue to
rely on plastic bottles for various purposes, the industrial
methods described herein ensure efficiency, consistency, and the
ability to meet the ever-growing demand for this ubiquitous
packaging solution.
Get our Practical Training guide on how to set up a lucrative
Pet Bottle Manufacturing Business in Nigeria. The Plant will
have the total installed output capacity of 24,000 PET bottles
Blowing Capacity per day working for 8 hours daily and 320 days
in a year. However production commences at 80% of the installed
capacity in the first year and increase thereafter until full
production capacity is achieved. The Plant will handle PET
Bottles Blowing for clienteles for the 500ml, 750ml and the
1,500ml Plastics types.
The Plant has been designed to use compact and cost efficient
PET blowing Machinery originating
from China. The expertise for the plant are available
locally. The detailed and comprehensive report according to
scale of production cover can be made available to you on
request. It will cover all the aspects of the project, from
analyzing the market, confirming availability of various
necessities such as plant & machinery, raw materials,
manufacturing techniques and forecasting financial aspects by
estimating the cost of raw material, formulating the income
statement, balance sheet and cash flow.
Click here to fill our application form:
https://forms.gle/jt7DaqkmobimT5PX8
One on one practical training with ongoing support
from our resource person. Well-crafted training
initiatives aim to close skill gaps, thus boosting
individual performance. The success of this program
reflects our shared commitment to creating a better
future for our participants The trainees are evaluated
at the end of the training period to ascertain the
reliability of such training so as to assist in the
provision of necessary instrument needed for starting
the business or trade. Training is built on an active,
experimental and practical learning sessions. Our expert
advice is unique, actionable, and impossible to
replicate. No one else can provide the tailored insights
we offer, designed specifically for your success
.Imagine having a roadmap tailored just for you, guiding
you step by step toward your
career goals. Attendees will receive certificate
of participation at the end of the Training
Click here to fill our application form:
https://forms.gle/jt7DaqkmobimT5PX8 |
Our motivation is to see every Nigerian benefit from our
Unique Income opportunity, specially focused towards a
sustainable, entrepreneurial, and innovative future by
connecting them to new ideas and skills
Browse through our highly resource information
over 500 Business ideas.
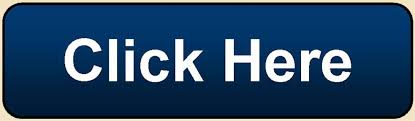
|
This guide is designed to help business people including Micro,
Small and Medium Scale Entrepreneurs navigate the legal and
regulatory considerations relevant to starting-up and doing
business in Nigeria.CLICK HERE |
Creating
multiple streams of income can be a strong way to improve
your personal finances. Whether you’re trying to boost your
savings or build toward a goal, this is a move that many of
the most financially successful Nigerians make.CLICKHERE |
|
© All rights reserved 2024. 21st Strategies Consulting Nigeria
|