How to start a Lucrative Cement Manufacturing Business in
Nigeria
Cement is the basic raw material of concrete and is a very
important building material.
The
manufacturing process of cement is rather complicated. It
consists of raw materials mining, raw meal preparation, clinker
calcinations, cement grinding, and some auxiliary operations.
Meanwhile, a large amount of dust and exhausted gas are
generated in the cement production process, so the cement plant
should also be equipped with complete sets of a dust control
system and waste heat power generation equipment. Therefore,
even the construction of a small cement plant can be counted as
a large-scale engineering project, and we must go through
thorough investigation and careful planning before starting a
new cement factory.
Nigeria currently faces a supply-demand gap of over 20 million
metric tonnes for cement. This deficit continues rising annually
by 10-15%. Furthermore, over 90% of cement sold comes from just
two major players, indicating a market dominated by monopolies
without enough competition.
As a new entrant, these statistics highlight the significant
margins and growth runways available within Nigeria’s cement
sector. The federal government aims to improve infrastructure
across transportation, housing, agriculture, and power. These
ambitious development goals will require vast cement quantities,
translating to widened opportunities.
1. Clarify Your Production Scale and Cement Type
The first thing to do when you are planning to start a cement
factory is to determine which type of cement you are going to
produce and how many tons you are going to produce per day
The most widely used cement for concrete works is ordinary
portland cement (OPC), apart from that, there is also pozzolana
portland cement (PPC), white portland cement, quick-setting
cement, refractory cement, etc.
The
production capacity of cement factories also varies greatly,
ranging from 50 TPD to 10,000 TPD.
What kind of cement does the cement factory produce? What is the
production scale? To answer these questions, investors must
consider the local cement market size, cement prices, and their
own investment capacity. The larger the production scale of a
cement factory, the higher the construction cost and production
cost. However, if the local cement demand is large and the
market competition is weak, then high output means high income
and profit.
2. Find the Most Appropriate Location for Your Cement Factory
The site of a cement factory is better near the limestone mine.
Cement plant locates near the limestone quarry.
The site selection of a cement factory is very important. A good
site can make construction easier, save construction costs and
subsequent production costs.
Since
the coverage area of a cement plant is very large and the cement
industry produces heavy pollution, cement plants are usually
built in the urban periphery or rural areas. And in most
countries, approval from the local government is required to
start a cement factory. The cement plant should also be as close
to the limestone mine as possible to save the transportation
cost of raw materials.
The
site of a cement factory cannot be selected easily. It needs a
professional team of engineers to investigate the local
geological environment and soil before finally determining the
appropriate site, and you can always rely on AGICO to find the
most appropriate site for your cement factory.
3. Design the Cement Factory
As a large-scale industrial facility with complex structures and
numerous machinery, the design and layout of a cement plant must
be entrusted to the professional engineering design institute.
The design institute is the cooperative unit with the longest
service time and the widest content for the project. The whole
process of project construction cannot be separated from the
cooperation of the design institute. Selecting an experienced
design institute is very beneficial to the quality, investment,
and progress of the project. The experienced design director
will assist the construction team to make the project plan and
remind the start-up time of each work.
4. Purchase Needed Equipment
This ball mill has been loaded on a track for transportation.
A cement ball mill is ready for transportation.
There are many kinds of industrial equipment used in a cement
plant, including thermal equipment, grinding equipment, dust
removal system, transportation system, storage system, and so
on. When placing an order, we may need to order different
equipment from multiple manufacturers at the same time.
Some large-scale equipment in the cement plant, such as cement
ball mill, vertical roller mill, cyclone preheater, rotary kiln,
etc., has a complex structure and takes a long time to
manufacture, so they must be ordered in advance according to the
schedule of the construction period to ensure that they will
arrive in time during the installation.
The supplier of each type of equipment should be selected in
advance to make sure the design institute will have sufficient
time to communicate with them to determine the parameters of the
equipment.
5. Factory Construction & Equipment Installation
The construction of a cement plant
The cement factory is under construction.
Once the overall structure design of the cement factory is
completed, then it is ready to start building. The civil
engineering and equipment installation of a cement factory are
undertaken by two different professional teams.
After the civil engineering team starts working, it is necessary
to check its construction organization and plan according to the
design progress. There must be a detailed work breakdown for all
the key sub-items. The equipment installation team is usually
called one to two months after the start of construction. They
need to cooperate with the civil engineering team to complete
the foundation construction of large equipment and complete the
installation of various machinery and systems.
6. Staff Recruitment & Training
The training of workers should start 2 months before the factory
project is fully completed. Because workers are better to be in
positions in the later stage of equipment installation and
single machine commissioning, to get familiar with their
positions and the machines they will be operating, so as to lay
a good foundation for future operation and maintenance.
Selecting the Cement Plant Location
Cement plants represent substantial fixed cost investments, so
choose an appropriate location from the outset. Conduct
feasibility studies around raw material availability, logistics,
labor, power access, water, housing, and connectivity.
Prioritize locations offering abundant limestone deposits, low
logistical costs, reliable infrastructure, and favorable
governmental policies. Analyze the proximity of major cement
consumers like state capitals and high-density housing areas.
Determining Required Capital Investment on a large Scale
The cement business is highly capital intensive. Starting a
plant entails securing:
Land
Plants and heavy machinery
Technology licenses
Logistics infrastructure like ports
Operating capital
Contingency funds
Realistically, you need at least $100 million to start a cement
company in Nigeria. This capital works as follows:
Equity: Gather 30% capital from investors and promoters
Debt: Raise 60-65% through banks/NBFCs
Working Capital: Remaining 10-15%
Storage and Warehousing
A small-scale cement manufacturing unit will also need
investments for storage and warehousing. Explore different types
of warehouses and pick the suitable one that helps maintain the
quality of raw materials and finished cement.
A rough estimate is $300,000 USD but it can vary depending on
several factors, including:
Location of the plant.
Choice of technology and equipment.
Land acquisition and development costs.
Fluctuations in raw material prices.
Regulatory requirements and compliance costs.
Conduct thorough market research and obtain detailed quotes from
suppliers and contractors to get a more accurate cost estimate
for your specific project.
Let’s explore the key storage components and considerations for
mini cement plant manufacturers who may want to invest in
storage and warehousing.
Key Storage Components for a Mini Cement Plant
Feeding Hopper with Load Shell: Temporarily holds and meters raw
materials before grinding.
Master Hopper: A larger storage unit that feeds raw materials to
the feeding hopper, ensuring a continuous flow.
Fly Ash Storage Silo: A tall, cylindrical structure for storing
fly ash in bulk.
Cement Silo: A large, vertical, cylindrical structure
specifically designed for storing finished cement.
Key Considerations
Capacity: The size and number of storage units depend on your
plant's production capacity and inventory needs.
Material Compatibility: Choose storage materials that are
resistant to the corrosive nature of cement and fly ash.
Safety: Implement dust suppression and proper ventilation to
ensure a safe working environment in storage areas.
Accessibility: Design storage facilities for easy loading and
unloading of materials, minimizing labor and equipment
requirements.
cta 2
Setting up a successful cement business in Nigeria needs
extensive planning, sizeable capital, strategic partnerships and
efficient execution. Find your competitive advantage through
cost leadership, targeted differentiation or geographical
dominance. Despite the complexities involved, significant
long-term profits make cement manufacturing worth the effort for
patient entrepreneurs.
Get our Practical Training Guide on How to start a Cement
Manufacturing Business in Nigeria. If you are planning to enter
the cement industry but don’t know where to begin with, We will
provide you with the step-by-step guide on how to start a cement
factory. The cement
industry presents massive opportunities, given the country’s
rapid urbanization and infrastructure development. This
step-by-step guide will walk you through the process of
establishing a successful cement manufacturing business company
from scratch in Nigeria. Thorough studies will help devise
precise business plans on product types, pricing, locations,
target markets, and financial modeling. Our experienced team
guides you through every process step, from initial design and
engineering to construction, commissioning, and handing the key
to start the production process
Click here to fill our application form:
https://forms.gle/jt7DaqkmobimT5PX8
One on one practical training with ongoing support
from our resource person. Well-crafted training
initiatives aim to close skill gaps, thus boosting
individual performance. The success of this program
reflects our shared commitment to creating a better
future for our participants The trainees are evaluated
at the end of the training period to ascertain the
reliability of such training so as to assist in the
provision of necessary instrument needed for starting
the business or trade. Training is built on an active,
experimental and practical learning sessions. Our expert
advice is unique, actionable, and impossible to
replicate. No one else can provide the tailored insights
we offer, designed specifically for your success
.Imagine having a roadmap tailored just for you, guiding
you step by step toward your
career goals. Attendees will receive certificate
of participation at the end of the Training
Click here to fill our application form:
https://forms.gle/jt7DaqkmobimT5PX8 |
.
Our motivation is to see every Nigerian benefit from our
Unique Income opportunity, specially focused towards a
sustainable, entrepreneurial, and innovative future by
connecting them to new ideas and skills
Browse through our highly resource information
over 500 Business ideas.
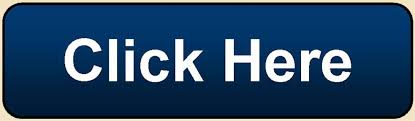
|
This guide is designed to help business people including Micro,
Small and Medium Scale Entrepreneurs navigate the legal and
regulatory considerations relevant to starting-up and doing
business in Nigeria.CLICK HERE |
Creating
multiple streams of income can be a strong way to improve
your personal finances. Whether you’re trying to boost your
savings or build toward a goal, this is a move that many of
the most financially successful Nigerians make.CLICKHERE |
|
© All rights reserved 2024. 21st Strategies Consulting Nigeria
|